Paper packaging is a sustainable, reliable, and cost-efficient way to transport and protect a wide range of products like groceries, medicine, animal feed, and cement.
Many types of paper-based packaging are widely accepted for recycling across the U.S.
Types of Paper Packaging
Cardboard and Paperboard
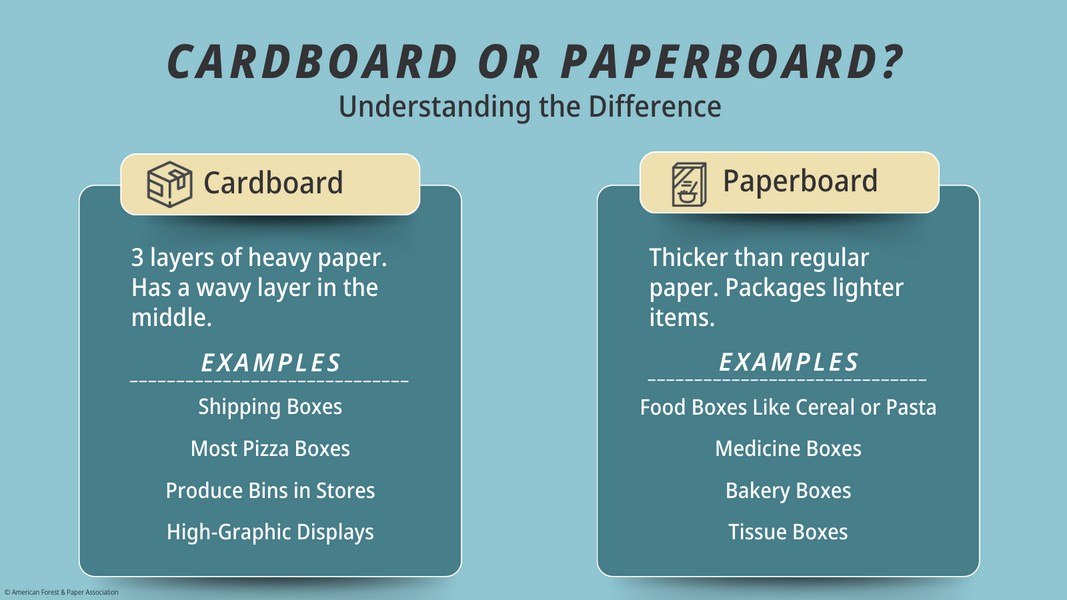
Cardboard
Cardboard is called containerboard and corrugated within the paper industry.
Cardboard is made of 3 layers of thick, heavier paper. The outside layers are flat and between them is a wavy, fluted medium. Cardboard is generally used to package heavier items.
Examples of cardboard include:
- Shipping boxes
- Most take-out pizza boxes
- Point-of-purchase displays to hold things like snacks
- Produce bins in stores
- Larger electronics like TVs
Paperboard
Paperboard is also known as boxboard within the paper industry.
Paperboard is thicker than regular paper but not as thick as cardboard. This material is used to package lighter items or create more intricate unboxing experiences.
Examples of paperboard include:
- Dry food boxes like cereal and pasta
- Small electronics boxes like phones or watches
- Medicine boxes
- Bakery boxes
- Tissue boxes
Did You Know
View the StudyA life cycle assessment from the Fibre Box Association showed substantial reductions in the environmental impacts of cardboard boxes.
The study shows a 50% per unit reduction in greenhouse gas emissions between 2006 and 2020.
Paper Bags and Shipping Sacks
Paper Bags
Paper bags are the only bags that are recyclable in curbside bins.
They are a sustainable, clean, hygienic, and convenient choice. They can also be used in a variety of ways.
Examples include:
- Grocery bags
- Lunch bags
- Take-out food bags
- Pharmacy bags
- Retail shopping bags
Paper Shipping Sacks
Shipping sacks are also referred to as multiwall sacks. They are made from more than one layer of paper and other protective barriers.
Paper shipping sacks are ideal for shipping bulk materials like agriculture, construction and everyday goods.
Shipping sacks package things like:
- Pet food
- Cement
- Bird seed
- Flour and sugar
- Grain
- Potatoes
Member Spotlight
Learn More About EarthKraft™Georgia-Pacific developed EarthKraft™, an all-paper padded mailer that is 100% curbside recyclable. The mailer was developed through collaboration with a major online retailer.
Additional Packaging
Food Service Packaging
Paper packaging is used in the food service industry too. Paperboard is generally used to create this type of packaging.
Examples include:
- Paper cups
- Burger boxes
- Fry containers
- Popcorn buckets
Paper-Padded Mailers
The recently developed innovative paper-padded mailers are made with 2 layers of paper and cushioning between the layers. These mailers are also curbside recyclable!
The cellulose-based cushioning material might look like “glue dots.” It is designed to separate from the paper easily and gets filtered out in the repulping process.
Did You Know
Learn More About Paper Cup RecyclingAcross North America, more than 40 mills can recycle paper cups and turn them into new products. The number of cities accepting paper cups is growing too.
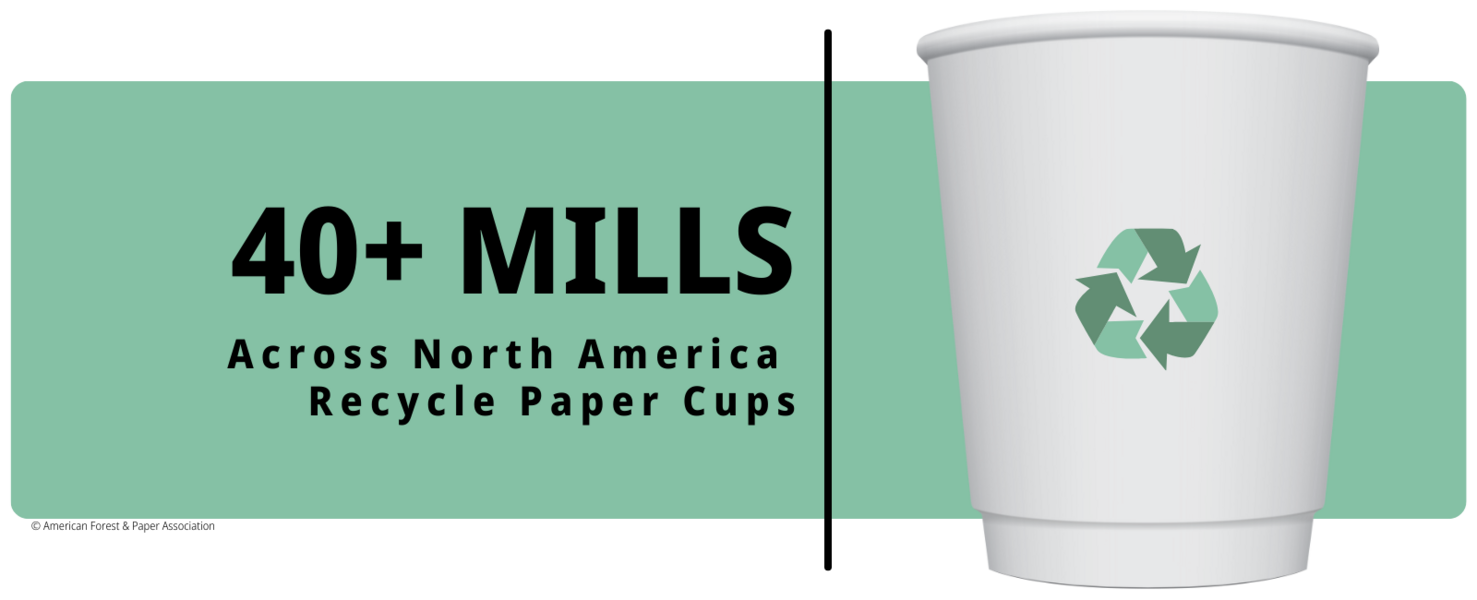